| |
Heat Damage
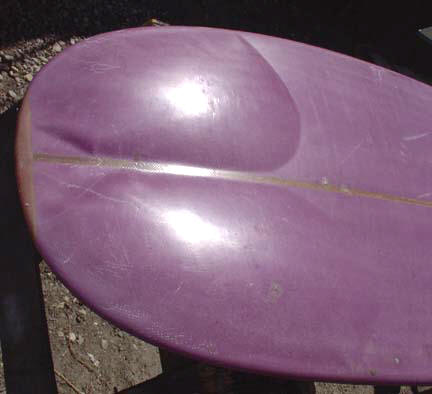 |
kind 'a cute, actually
and provoked all manner of hilarity as it reposed on my
racks
but the owner of this almost new custom extruded EPS
board was not amused |
Most everything in our
daily lives is heat sensitive. We know better than to leave the dog locked
in the car on a warm summer day. We know better than to leave a cake of wax
on the dash, or a can of pop. But for some reason, people continue to be
surprised when their boards blow up after having been exposed to that same
sort of heat. Most materials change their molecular structure when heated
dramatically. So does the EPS foam in Epoxy
boards. As it changes, it releases prodigious amounts of gas. That gas has to
go somewhere. It will make itself room. It will blow a bubble. Or two - see
above. So keep it cool! If you are comfortable,
so is your board. If you feel sick from heat, so does your board. If you
leave your board in a dark car, windows up, and the outside temperature is
95 degrees, the inside of your car may well go above 130 degrees. EPS foam
outgasses at 130 degrees, Divinycell shrinks markedly at 130 degrees,
room-temperature-cure Epoxy
resins turn brittle at 130 degrees. The result at minimum is a reduced
lifespan of your board. You may get away with a printing through of the
reinforcements and inserts. But you may well end up with a bubble.
So - how come these problems are just localized?
Localized bubbles are usually the result of concentrated heat. I have seen
boards transported on top of hatches on motorhomes, where the
glazing reflected the sun's heat onto a square patch of board, producing a
square bubble. Also, if a board is fatigued, a general heating up can cause
a locally fatigued spot to blow. Or it can be a combination, such as when my
Olde Trusty blew an aneurysm while waiting for wind under a blue tarp.
Mid-bottom had already delam'd in a few places, and it gave way this time
where the tarp touched the bottom, creating a patch too hot to touch.
Keep it cool!!
|
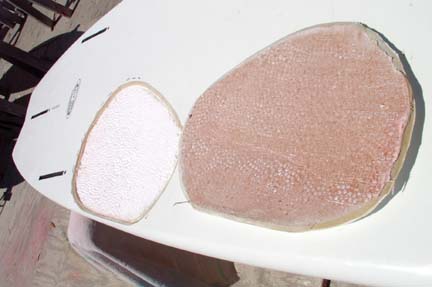 |
not quite as picturesque a bubble as the purple one above
all ingredients were properly processed, adhesion was good between layers,
there was no contamination, no cavities |
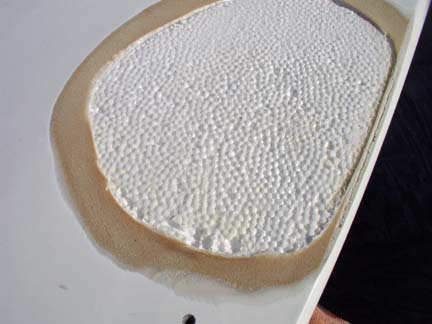 |
the cause was unequivocally heat, as evident by the altered
structure of the EPS foam: the "fluff" surrounding the foam beads shrunk,
leaving the beads standing proud. Instead of a satin-y feel, the surface
feels scratchy, i.e. the material turned brittle.
These changes require at
least 130 degrees of heat. At 130 degrees, EPS out-gasses strongly, blowing
the "lids" off things, distorting boards, and generally wreaking havoc.
smooth, healthy EPS at top of cut-out; shrunk, heat-damaged
EPS bottom 3/4s |
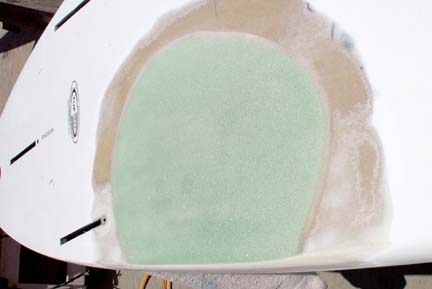 |
The fix: bevel-grind the edges, vacuum-bag new inner glass &
PVC foam |
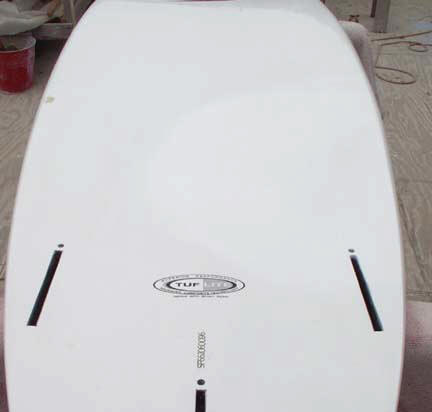 |
glass over, fair, prime, coat w/ LP, rub out, and send home with a stern
lecture about keeping the board away from extreme heat. |
return to
Miscellany |
|