| |
Starboard Acid Rail
Repair |
|
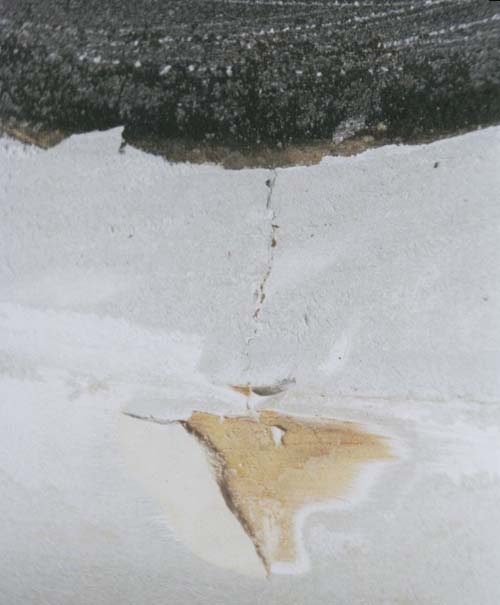 |
On the rail, outboard and
beneath the forward heel bumper, a vertical crack. Beneath, covered by some Marinetex, a horizontal (longitudinal) crack, that was the first indication
of trouble, according to the owner. With thick
padz, plus the extra bumper, it is hard to feel any structural softness. It
does, however, make crunchy sounds when pushed with the thumb. |
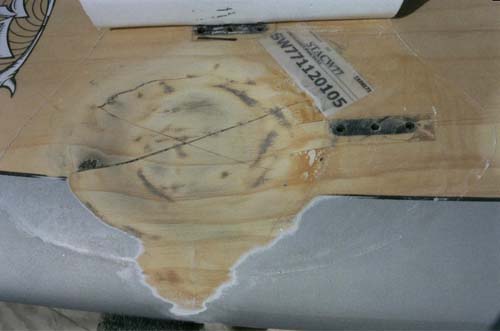 |
All EVA and paint removed
for inspection. The criss-cross pattern in the
veneer is factory, to facilitate the veneer conforming to the deep recess.
The veneer crack upper left quadrant probably
happened during manufacture - unfortunate, but not a great diminution of
panel stiffness (the veneer's major function). The sand-through at 8:30 is
similarly insignificant, since it is located in a spot of great inherent
stiffness due to its shape. |
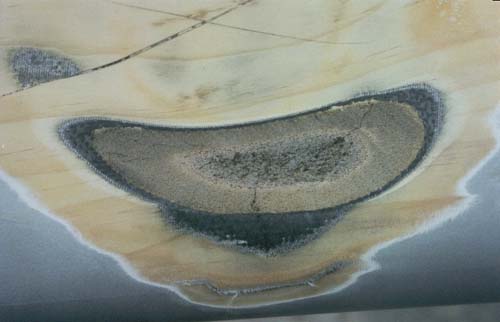 |
Grinding down through the
layers in search of sound material. Beneath the
veneer some Carbon cloth - fractured. Beneath that some 4.5# density
Divinycell - fractured. Beneath that some what appears to be 3# density
Divinycell, also fractured. |
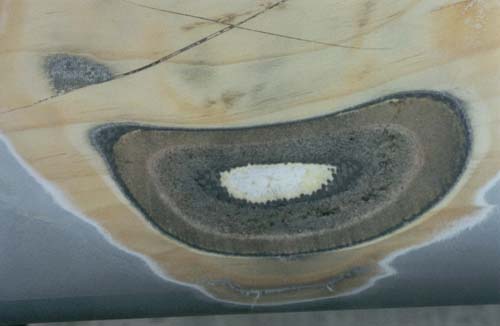 |
Beneath the inner, lower
density Divinycell, more Carbon cloth, also fractured. Finally, beneath the
inner Carbon, the EPS - sound, albeit damp.
With all layers contributing to the strength, it is vitally important to
remove and replace all failed components of a composite, not just the
outermost layers! |
 |
After drying, new inner
Carbon cloth and Divinycell are vacuum-bagged and shaped, new outer Carbon
cloth and veneer are vacuum-bagged and feathered out. |
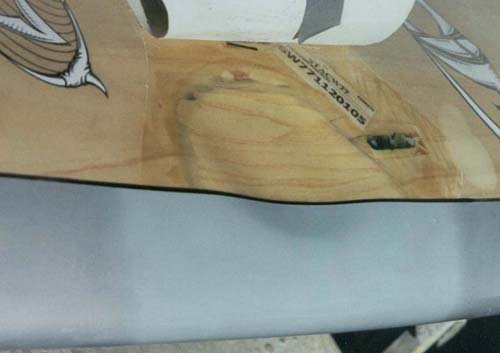 |
To eliminate all
possibility of water absorption into the veneer, I saturate it with
penetrating Epoxy, then glass over with 3.2oz cloth in UV-resistant Epoxy.
The factory chooses not to do this, settling for an Acrylic clear-coat
instead. For boards that live in hot, dry climates, this frequently means
splitting veneer and discoloration. |
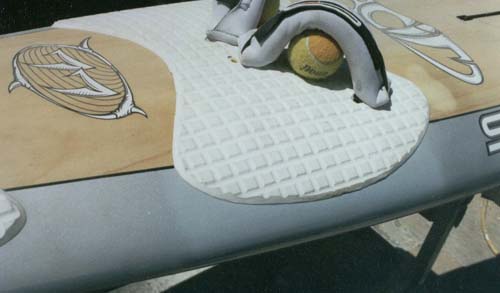 |
After reinstalling bumpers
and padz, I touch up the non-skid by misting Acrylic dust into clear Acrylic
paint. |
back to
Repair Menu |
|